
町工場にIoTを導入したいけど、そもそもIoTで何ができるのか、IoT導入のために何をしたらいいのかわからない、という方も多いと思います。
このブログでは、そのような方に向けて、さまざまな分野から、IoT導入事例をいくつかピックアップして、紹介していこうと思います。
今回は、早期からIoTを導入している等、先進的な取り組みを行っている中小製造業の導入事例を紹介します。
いずれも、IoT導入に関してはとても有名で、ネット記事などでもよく見かける企業の取り組みです。
IoTの各技術要素について
IoTでは、「デバイス」でさまざまなモノからデータを採取し、そのデータを「ネットワーク」を使って「サーバ」に送り、そこで蓄積・活用します。
また、デバイスは、モノから実際にデータを採取する「センサ」と、採取したデータを処理してネットワークに送る「プロセッサ」で構成されます。
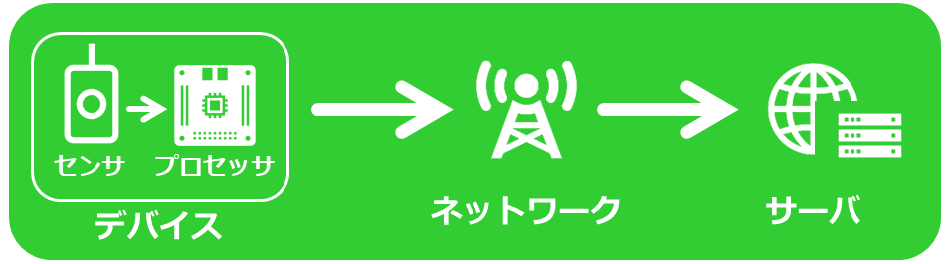
ここでは、各企業がどのような「センサ」「プロセッサ」「ネットワーク」「サーバ」を使っているか?に着目して紹介します。
久野金属工業株式会社
愛知県常滑市に本社がある久野金属工業株式会社は、従業員数352名の企業で、自動車用及び産業用部品の開発〜量産を行っています。
こちらの企業では、関連会社(ソフトウェア開発)が開発したIoTシステムを自社ラインに導入することで、装置の稼働状況の「見える化」を実現しています。
具体的には、工場の稼働状況を把握するために、加工ラインの一部にIoTデバイスを取り付け、社員がスマートフォンなどで稼働状況を確認できるようにしました。
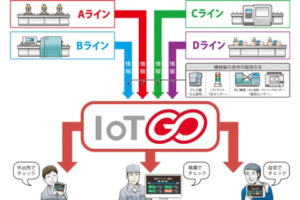
デバイスで取得する情報をON/OFFだけに絞り込むことで、古い機械からも簡単にデータ収集が行えるようにしました。
これにより、プレス機の平均稼働率が、導入前の32%から、導入1カ月後には55%、導入3年後には71%に上昇しました。
また、データがあることで、製造部門だけで改善活動ができるようになりました。
デバイス(センサ)は「光センサ」など、ネットワークは「Wi-Fi」と「LTE」、サーバは「クラウドサービス(Microsoft Azure)」を利用しています。
旭鉄工株式会社
愛知県碧南市に本社がある旭鉄工株式会社は、従業員数480名の企業で、自動車部品を製造しています。
こちらの企業では、製造ラインにおける生産個数や稼働時間(設備の停止時間)などの情報をリアルタイムに自動で検出し、スマホなどで見える化するIoTシステムを自社開発しました。
開発方針は「必要最低限のデータのみ取得する」「初期投資を安価に抑える」こととし、秋葉原のパーツショップで売られているような汎用部品を活用し、安価に自社で開発しています。
また、2016年には、開発したIoTシステムを外販するために子会社を設立しています。
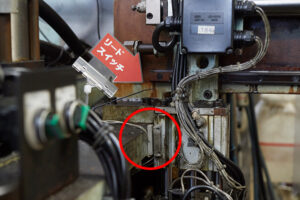
社内の100ラインに導入し、平均で約43%の生産性改善を実現しています。工程内不良率も劇的に低下し、品質向上にもつながったとのことです。
デバイス(センサ)は「光センサ(3色信号灯の点灯状況を取得)」「磁気スイッチ(装置の動作や扉の開閉情報を取得)」など、 デバイス(プロセッサ)は「Raspberry Pi」、ネットワークは「無線」、サーバは「クラウドサービス(Amazon Web Service)」を利用しています。
武州工業株式会社
東京都青梅市に本社がある武州工業株式会社は、従業員数157名の企業で、自動車用金属パイプ部品加工などを行っています。
こちらの企業では、加工機の動作箇所に「iPod Touch」や古いスマホを貼り付け、スマホ内蔵の歩数計機能(加速度センサ)で装置の動作回数を自動計測するシステムを自社開発しました。
そのデータを使って、機械の稼働時間や停止時間の分布、加工時間に関する分析を実施できるようにしました。
また、機械が停止した際には、加工機に貼り付けているスマホの画面上から、停止理由を手入力(メニューから選択)できるようにしました。これにより、停止時間の理由別分布も分析できるようになりました。
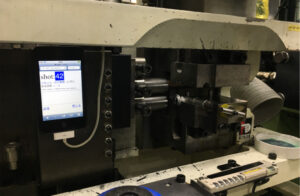
分析データを元に、工員の作業改善や機械の早めの修理などの対策を講じることで、生産性が従来よりも20%向上しました。
デバイス(センサ)は「スマホ内蔵加速度センサ」、デバイス(プロセッサ)は「スマホ」、ネットワークは「Wi-Fi」、サーバは「クラウドサービス(Amazon Web Service)」を利用しています。
株式会社トーア紡コーポレーション
大阪府大阪市に本社がある株式会社トーア紡コーポレーションは、従業員数472名の企業で、繊維製品の製造販売などを行っています。
こちらの企業では従来より、電力会社とのオンデマンド契約により、使用電力の管理が必要となっていました。
契約上限を超えないよう、電力の利用抑制や一時的な発電機利用などを行うのですが、電力使用量が増大する夏場には管理者の負荷が増大するため、「電力利用量データを誰でもチェックできる」仕組みを構築しました。
具体的には、CTクランプ対応の電力量モニタ、携帯電話網を利用する通信デバイスを活用することで、製造装置の改良や工場停止などを行わずに、古い装置にも導入することができました。
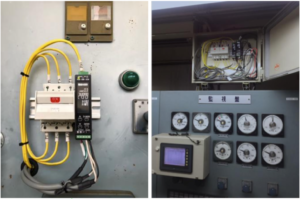
構想2ヶ月、設置作業1週間で運用を開始することができ、夏場の電力ピーク抑制で成果を上げることができました。
デバイス(センサ)は「CTクランプ対応電力量モニタ」、デバイス(プロセッサ)は「市販のIoT端末(株式会社 KYOSOのMORAT GW)」、ネットワークは「SORACOM Air(携帯電話網)」、サーバは「クラウドサービス(Amazon Web Service)」を利用しています。
まとめ
いずれの企業も、課題や目標を明確にし、自分たちで主体的にIoT導入に取り組んでいます。
また、あまり高度な技術は使わず、自分たちでできる手段で、効果が最大限に得られる方法を見極め、それを実践しています。
やはりこの辺りが、IoT導入を成功させるポイントのようです。